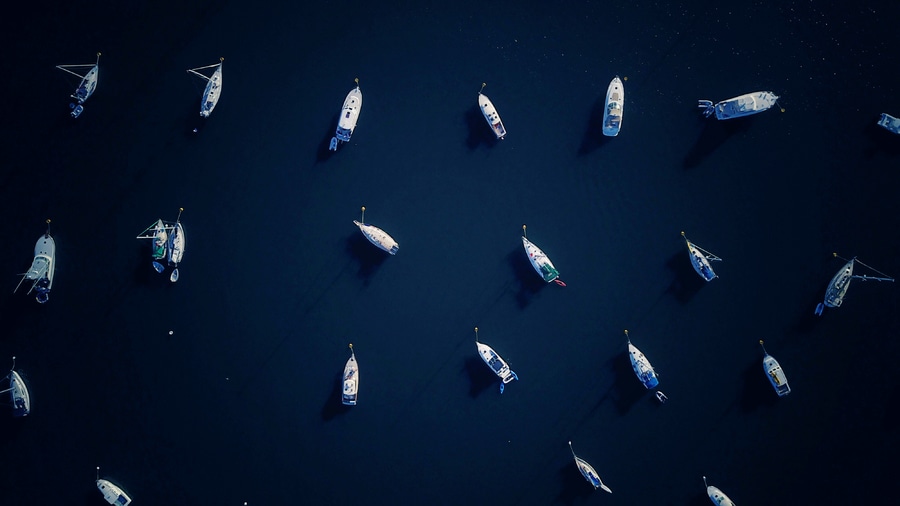
#Industry News
Blade Cells vs. Prismatic LFP Cells: Advancing Battery Technology in the Marine Industry
As the marine industry continues its transition toward electrification, battery technology sits at the heart of innovation. Among the lithium iron phosphate (LFP) options available, two formats are currently under the spotlight: traditional prismatic LFP cells and the newer blade cell design.
1. Enhanced Safety – A Crucial Factor at Sea
Safety is paramount in marine environments. Blade cells are designed with a slim, elongated structure that allows for better heat dissipation and improved thermal runaway resistance. In rigorous testing, blade cells have been shown to withstand punctures, crushes, and even nail penetration without catching fire—a stark contrast to many prismatic designs.
For vessels operating in remote waters or carrying passengers, this added thermal and structural stability significantly reduces fire risk, improving overall onboard safety and insurance profiles.
2. Higher Energy Density in Pack Configuration
While individual blade cells may not always have higher energy density than prismatic cells on a per-volume basis, their form factor allows for more efficient packing. In marine battery enclosures—where space is often limited—blade cells can be tightly stacked to maximize usable energy within the same footprint.
This leads to longer range or more operational hours per charge, whether you’re powering an electric outboard motor, hybrid propulsion system, or onboard auxiliary systems.
3. Better Structural Integration for Marine Enclosures
Unlike traditional battery formats that require heavy and bulky casings, blade cells can be directly mounted into structural components. This opens the door to battery packs that double as structural elements in the vessel’s design, reducing weight and complexity.
For shipbuilders and marine system integrators, this means:
Simplified installation
Fewer components
Lower overall system weight
And in marine vessels, every kilogram saved means greater efficiency and better fuel economy (if hybrid) or longer range (if fully electric).
4. Longer Lifespan in Harsh Conditions
Marine environments are notoriously unforgiving—high humidity, salt exposure, and temperature fluctuations are the norm. Blade cells, by virtue of their robust construction and minimal internal resistance, tend to degrade more slowly under harsh conditions.
This means:
Longer service life
Reduced maintenance
Lower total cost of ownership (TCO)
Operators benefit from fewer battery replacements over time, which is particularly important in commercial fleets or off-grid applications like autonomous surface vessels or offshore monitoring platforms.
5. Improved Thermal Management
Thermal management is critical in any battery system, but especially so in marine environments where ambient cooling can be limited. Blade cells, thanks to their flat and uniform shape, provide greater surface area for heat exchange. This improves cooling efficiency and allows for simpler, lighter cooling systems onboard.
That’s a major plus when designing battery rooms or integrated electric propulsion systems where every bit of thermal performance counts.
Final Thoughts
While prismatic LFP cells have served the marine industry well, the blade cell format represents a significant leap forward—offering better safety, efficiency, and design flexibility. For vessel designers, operators, and marine tech integrators, this newer cell technology aligns closely with the growing demand for smarter, safer, and more space-efficient energy systems at sea.
As the marine industry continues to decarbonize, blade cells are well-positioned to become a cornerstone of the next generation of electric and hybrid vessels.