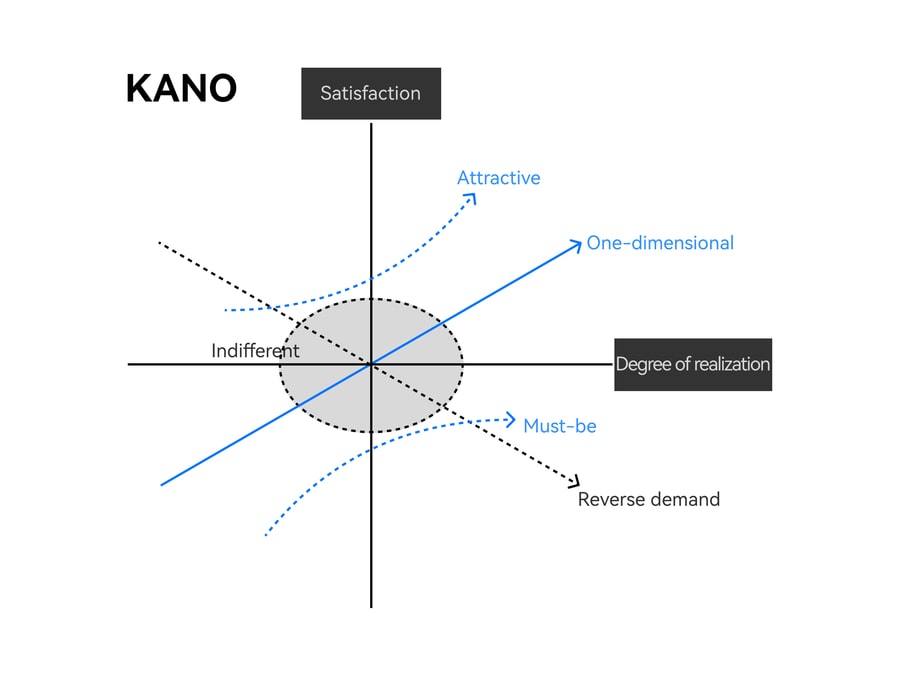
#Industry News
Design and Application of Ship Main Engine Control Handle Based on KANO Model
With the help of the Kano model, accurately identify the demand levels of crew members for the functions of the control handle, prioritize the satisfaction of key demands, and enhance the competitiveness of the product and user satisfaction.
I. Application Steps
1.Demand identification and questionnaire design
(1) Sort out the demand list: Explore from dimensions such as function, experience, and safety, such as single handle control, status feedback, anti-slip grip diameter, IP65 protection, modular customization, etc.
(2) Construct the Kano questionnaire: For each demand, design two "positive + negative" questions to inquire about satisfaction when the function is "present/absent", with five levels of options (very satisfied, taken for granted, indifferent, reluctantly accepted, very dissatisfied). Example:
① Demand for "single-handle control logic" :
② Forward question: "The control handle has a simple single-handle operation logic (integrated forward/backward/speed adjustment). What's your feeling about it?"
③ Negative question: "The control handle lacks a simple single-handle operation logic (requiring a combination of multiple buttons/knobs for operation). What's your feeling about this?"
------------------------------------------------------------------
2. Data collection and classification statistics
(1) Research subjects: Covering ship pilots, engineers, shipyard designers, etc., to ensure a comprehensive sample.
(2) Data organization: After collecting the questionnaires, calculate the option distribution of each demand under "with/without function", and determine the demand types (A - excited type, O - expected type, M - basic type, I - undifferentiated type, R - reverse type) :
①M Basic type: When the function is "present", users take it for granted; when it is "absent", they are "extremely dissatisfied" (for example, the status feedback shows that the absence of this function affects operational safety).
②O Expectation type: "Satisfied" when the function is "present", "dissatisfied" when it is "absent" (such as the anti-slip grip diameter design, which affects the operational comfort).
③A Excited type: "Very satisfied" when the function is "present", and "indifferent" when it is "absent" (such as intelligent fault diagnosis prompts to enhance operational convenience).
④I undifferentiated type: Users "don't care" whether the function is "present" or "absent" (such as cool RGB lighting, which has no substantial value for ship control).
⑤R reverse type: "Dissatisfied" when the function is "present", "satisfied" when it is "absent" (such as overly complex custom Settings, increasing the learning cost).
------------------------------------------------------------------
3. Demand priority ranking (calculating the Better - Worse coefficient)
Formula:
①Better Coefficient (Positive Satisfaction coefficient) : Better= (A+O)/(A+O+M+I), reflecting the degree of improvement in user satisfaction when needs are met. The closer the value is to 1, the stronger the positive impact.
②Worse coefficient (Negative Dissatisfaction coefficient) : Worse= -1 × (O+M)/(A+O+M+I), reflecting the degree of user dissatisfaction when demands are not met. The closer the value is to -1, the greater the negative impact.
(2) Priority conclusion:
① Basic requirements (such as status feedback display, single-handle control logic) : Both Better and Worse coefficients are high, and they must be prioritized to ensure safety and a basic user experience.
② Expectation-type demands (such as anti-slip grip diameter design) : The Better coefficient is relatively high, with secondary priority optimization to enhance satisfaction.
③ Excitation-oriented demands (such as intelligent fault diagnosis prompts) : With a medium Better coefficient but potential for differentiation, they are invested as innovation points to enhance competitiveness.
------------------------------------------------------------------
4. Design implementation and verification
(1) Function integration: Based on priority, basic requirements serve as the design bottom line (such as clear status feedback and simple control logic), expected requirements incorporate core interactions (such as optimizing the grip curve of the controller), and exciting requirements are highlighted functions (such as built-in fault diagnosis prompt lights in the controller).
(2) Prototype verification: Create a prototype of the controller, invite target users to try it out, and verify the satisfaction of requirements through the Kano model for the second time, and iteratively optimize (such as adjusting the feedback sound effect, grip material, etc.).
=========================================
II. Application Value and Precautions
1.Value
① Avoid overdesign: Eliminate undifferentiated demands (such as redundant appearance decorations) and focus on core functions.
② Balancing safety and experience: Basic demands ensure safety, while expectation and excitement demands enhance the operational experience.
③ Guide cost input: Prioritize resource investment in high-impact demands (basic and expected types), and control the cost of innovative functions.
------------------------------------------------------------------
2. Precautions
① Sample representativeness: It is necessary to cover crew members of different ranks and with different levels of experience to ensure comprehensive requirements.
② Demand dynamics: The iteration of ship technology may change the type of demand, and regular re-evaluation is required.
Through the Kano model, the design of the ship's main engine control handle can precisely anchor the core needs of users, taking into account safety, experience and innovation, making the design more in line with actual scenarios and user expectations.
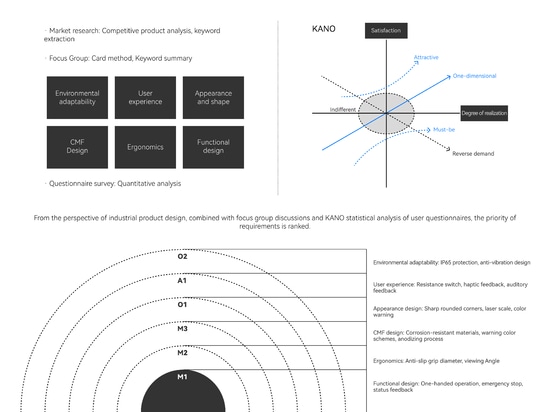