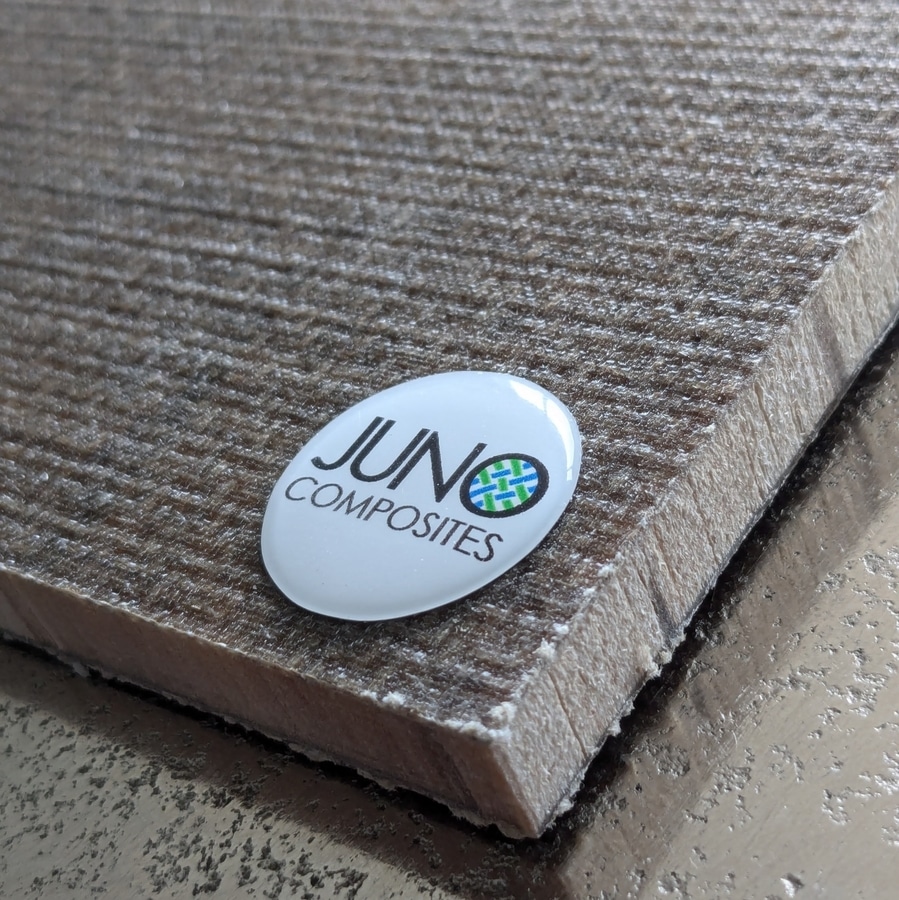
#Product Trends
Natural Fibre Reinforced Bio-Based Polymer Composites
All natural composite panels developed for naval sector
Recently, Juno investigated the mechanical performance of flax reinforced composites with novel epoxy resin synthesised in the VIBES project that are mostly comprised of bio-derived precursors. The VIBES project has produced novel epoxy resins synthesised by Specific Polymers (France) and flax reinforcement textiles woven by FLIPTS & Dobbels (Belgium). Juno manufactured composite test panels from the constituent materials developed in the VIBES project including; flax reinforcements and bio-based epoxy matrices. We mechanically tested these novel composites with regards to their fibre and resin dominated properties and benchmarked their performance against composites that we manufactured with commercial-off-the-shelf (COTS) epoxy resin (Sicomin France) and flax textiles (ECO-Techlin).
In addition, Juno have investigated the effects of moisture content in the natural flax textiles and their negative impact on the mechanical performance of the final composite. Industrially suitable drying strategies (in the context of composite manufacturing e.g. resin infusion) need to be developed in order extract the maximum performance from natural flax fibre textile reinforcements for composites. Where test results indicate the typical ‘as-received’ moisture content of woven flax textiles to be 13-15% on average. Mechanical testing indicated that by implementing a more effective drying strategy for the textile flax reinforcements before they are infused with epoxy resin, achieving a moisture content below 1%, will result in higher performance values overall. Furthermore, this work has indicated that in order to maximise the performance/reduce variability of flax fibre composites and encourage transition to ‘greener’ and more sustainable composites, it is crucial to examine and record the fibre production during scutching, hackling and spinning prior to arrangement into textiles (woven and non-crimp fabrics) in order to fully understand how the performance of the flax textile might be enhanced for production of engineering composite materials as opposed to production of apparel. Presently, there is a lack of basic mechanical and physical properties that are made available from fibre and textile manufacturers of flax fibres and flax textiles to the composite material designers and fabricators. Successful optimisation of the final flax fibre composite requires the engagement of the whole value chain from the scientist’s selecting seeds/strains that promote the most favourable characteristics, farmers growing and harvesting the flax, the fibre processors, the textile manufacturers and the composite materials designers and fabricators.
Find out more from the link below