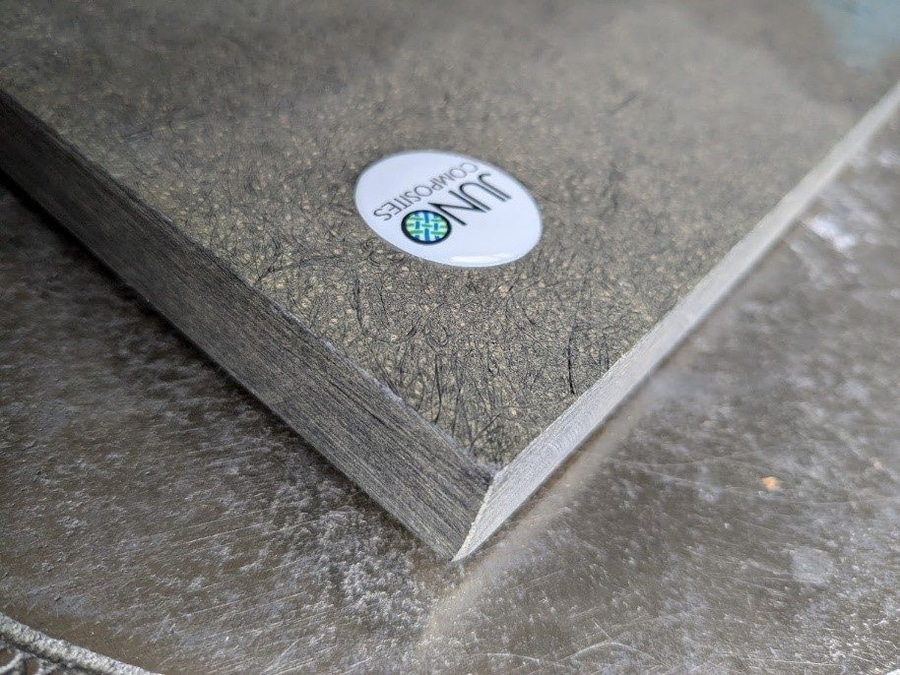
#Industry News
Sustainable fire retardant composites
Novel FST materials for the naval sector
The trend towards increased sustainability could soon become legislated requirements in the European Union, for example within the automotive sector, the ‘End-of-life vehicles Regulation; mandate that manufacturers need to declare the recycled vehicle content, 25% of plastic used for new vehicles must be from recycled feedstock along with other requirements that incentivise manufacturers to recycle more effectively and recover better quality raw materials (reference: https://environment.ec.europa.eu/topics/waste-and-recycling/end-life-vehicles/end-life-vehicles-regulation_en).
Climate change forces the aviation sector to develop and implement more sustainable material innovations for aircraft. For example, innovation in this sector in the coming years will seek more sustainable composite materials for aircraft interiors with emphasis on bio-based composite materials and materials that are recyclable after their useful life. This is particularly pertinent in the management of waste composite materials generated from the interior aircraft market, which are frequently replaced every 4 to 7 years [Zarnowka, 2023, Sustainability Assessment of a Sustainable Innovation for the Aviation Industry: Case Study of Bio Composites for Aircraft Interiors]. With applications such as aircraft interiors, there are safety critical properties namely fire retardancy where it is essential that research efforts look to develop bio-based and or recyclable phenolic type polymer matrices that achieve the necessary qualifications for fire retardancy (of the whole composite) whilst lowering their environmental impact. These in turn can be combined with recycled fibre reinforcements such as recycled carbon fibre and phenolic.
Figure 2: Bracket machined from 30mm thick recycled carbon reinforced phenolic matrix composite plate
High strength and modulus fibre reinforced advanced composites are important materials where characteristics can be tailored to offer, for example; high temperature performance, good vibration dampening, low coefficient of thermal expansion (CTE), fire retardancy and are essential in applications that prioritise lightweighting, which make them the obvious choice for transport applications. The composite material’s final performance can be designed as a function of:
1. The type of constituent materials used as the fibre reinforcement (e.g. carbon, glass, flax basalt) and polymer matrix (e.g. epoxy, phenolic, polyester)
2. The directional arrangement (e.g. quasi-isotropic) of the textile reinforcement form (e.g. woven, non-crimp fabrics etc.)
3. The manufacturing strategy used to bring the individual constituent parts together to form a new composite material e.g. Liquid moulding, prepreg method, Wet lay-up etc.
At Juno Composites we are investigating novel formulations of phenolic resins that are suitable for current state-of-the-art composite manufacturing techniques. Where these types of polymers although generally possess lower mechanical properties and chemical resistance compared with epoxy, are essential for applications where fire retardancy are of primary importance e.g. aircraft interior panels, offshore oil and gas, mass transit and electronics.
Juno Composites are currently developing a range of low free formaldehyde phenolic matrix fibre reinforced composites utilising recycled carbon fibres, continuous carbon & glass fibre textiles, natural fibre textiles that will become available in various material forms including; thin foils, sandwich core panels, sheets, plates and billets/blocks (for machining complex parts such as composite brackets). As part of the material design stage, aside from the mechanical and fire smoke & toxicity performance (FST), we are ensuring that the constituent parts (fibre reinforcement & polymer matrix) and the moulded composite part are more sustainable and are compliant to REACH.
Find out more with the link to the original article
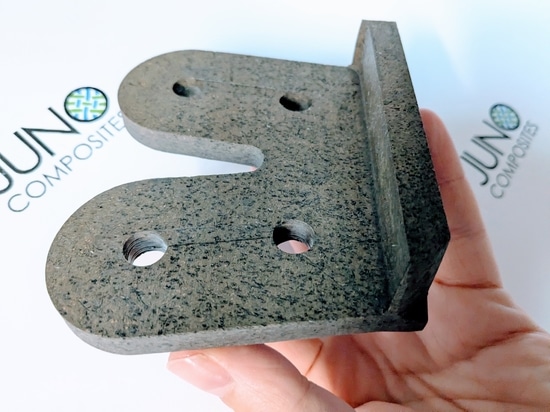